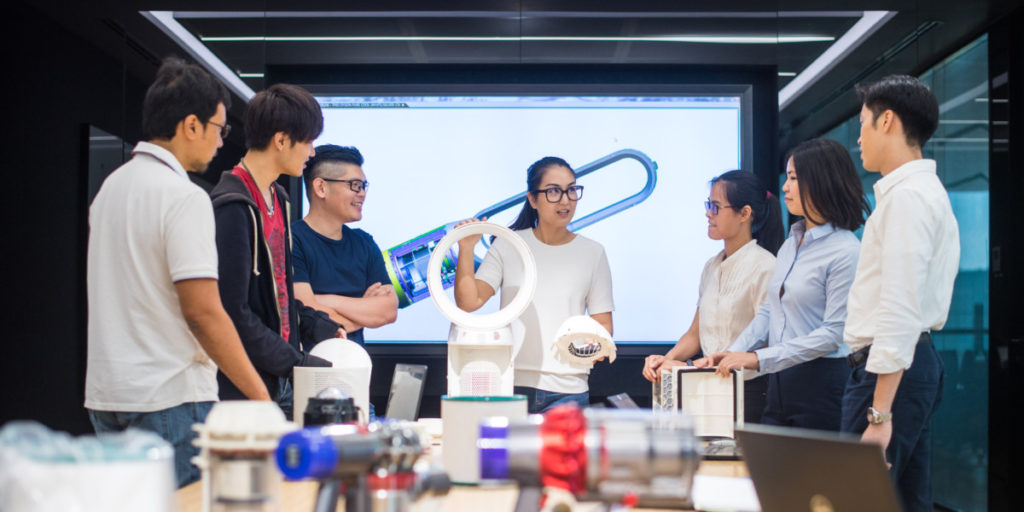
Dyson gives a glimpse of the future at exclusive R&D Lab Tour
“We’re here,” said the driver cheerily before the van door of the Toyota Vellfire silently slides open and we’re hustled out into the muggy dawn air of Johor Bahru at Dyson’s Malaysia Development Center, one of their largest and most important facilities in Southeast Asia.
Strategically located within an intricate web of suppliers and just within reach of the docks of Pasir Gudang and but a stone’s throw away from Singapore, the Dyson Malaysia Development Center is not only a strategic hub for Dyson’s manufacturing operations, it is also one of their most important Research and Development centres on the planet.
Hosts of buildings are sprawled across the multi-football field spanning MDC campus, dedicated to bringing Dyson’s next generation of products to life and to ensure their present ones are constantly tested to ensure they continue meet the phenomenally lofty standards that the brand is known for. And it’s here that we’re granted the privilege of seeing how much effort and to what lengths Dyson would go to in order to create their world renowned products such as their recently released V10 cordless vacuum cleaner.
The anteroom, where a team of receptionists sat waiting to greet us was sparsely but thoughtfully decorated with a selection of Dyson’s latest offerings, arrayed in two neat rows flanking the counter to the left and right. Among them was the recently launched V10 along with a smattering of their other offerings including their latest hair dryer and fans. After several minutes and a small mountain of tree-eradicating paperwork, we were finally let into the engineer’s equivalent of the Willy Wonka Chocolate Factory.
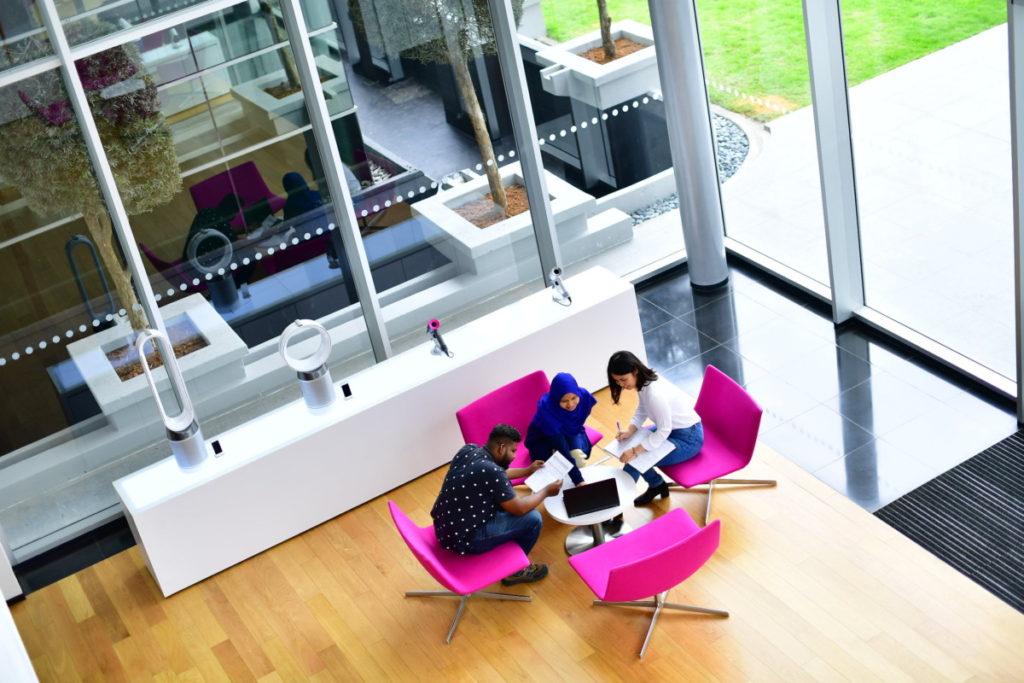
The anteroom of the Dyson MDC
Through the white door
We strode past a swinging white door and through another set of doors, this one further warded with an ID tag by one of our chaperones before we then entered the proverbial rabbit hole proper. As we walked down a neon lit corridor, we were filled in verbally on what our guided tour would entail. Each of the labs was specialised in form, function and personnel to test for a particular aspect of a product and each varied in size with some spanning the length of a football field.
Our first test lab and first port of call hit us with a wall of noise as a cadre of earmuff-wearing, masked staff diligently shuffled about a concrete-shod floor doing terrifying things to a selection of Dyson’s latest products including their hair dryers and vacuum cleaners. If there was a purgatory for appliances, this was it as each one was subjected to a battery of physical tests to simulate normal wear and tear.
One staff member took great pains to drop a Dyson hair dryer from waist height in different positions, repeatedly and then diligently recorded her findings on a blotter nearby. What was intriguing was that it was done with the clinical approach of a methodical scientist out to determine something and in this case the ultimate durability of the product.
Another test crew methodically slapped the head of vacuum down on the floor to simulate rough use or someone with questionable depth perception with an audible slap. In other parts of the complex, Dyson appliances are hooked up to automated test rigs to simulate charging and discharge cycles akin to years of usage accelerated to weeks to test for any flaw during the course of their lifespans.
For someone used to taking care of their equipment so that they could last as long as possible, the sight was disconcerting indeed. It was also ultimately necessary as Dyson aims to make sure their products stand up to normal use, wear and tear and are able to go the distance. In a way, it was reassuring to see that whatever Dyson puts out into the market, it’s designed to survive almost anything the most ham-fisted user can subject it to.
Another test chamber was a complete antithesis of the first and rather than an aural pandemonium, it was silent enough to hear a pin drop. As part of their efforts to produce more powerful yet quieter engines and other hardware, Dyson also takes active measures to enhance audio dampening and other techniques to make their devices run quieter. This echo recording chamber was how devices are tested to see how loud they were when in use.
Studding the walls of the test chamber were spikes made of fabric and foam to absorb noise along with a lattice of mikes arrayed in the shape of a hemisphere to record what noise and where exactly it took place in the room. A helpful engineer showed the difference between an older Dyson vacuum cleaner from a couple of years ago and the new V10. The difference is night and day with the older version sounding like a rattling can of peas by a frenetic child. The V10 was an order of magnitude quieter and while not whisper silent, was quiet enough that someone in a couple of rooms over would likely not even detect the noise.
Other chambers tested for all manner of other factors including efficient airflow through their products even when occluded by dust all the way down to obscure (to mere mortals like us) but nonetheless critical minutiae such as if a product would interfere or be interfered by radio frequency waves from another electronic device.
We got a sense of the scale and scope of the MDC as well as Dyson’s truly deep level of testing but the biggest surprise later on, after we were ushered out from the test labs was the chance to meet the man himself, Sir James Dyson as he shared his thoughts, dreams and ideas of the future.
A word with Sir James Dyson
Sir James Dyson, OM CBE, FRS FREng strikes a dignified air as he sits at the head of the table amidst a cohort of journos. The legend behind the man is almost mythical and the passion behind his work and his vision was apparent with every word he said.
With a measured pause, he then fielded our questions as to his brainchild around him, now a global brand with products is sold in almost every major city on the planet and what plans he has for the future and beyond, especially in regards to electric cars and autonomous driving.

Sir James Dyson fielding questions from journalists at the Dyson MDC
“Totally autonomous driving is some way off,” said Sir Dyson,”but that doesn’t mean that we can’t use some of the technology to make driving safer.” He added “The problem with autonomous driving is that the reaction time of the person in charge of the vehicle becomes much slower if they are not driving and their ability to react in a dangerous situation becomes slower. There are a lot of things for society to consider before we allow autonomous driving.”
On the note of developing vehicles, he then added a tempting detail about his ongoing project to develop a battery electric cars.”We are launching it in 2020 and delivering it in 2021.”
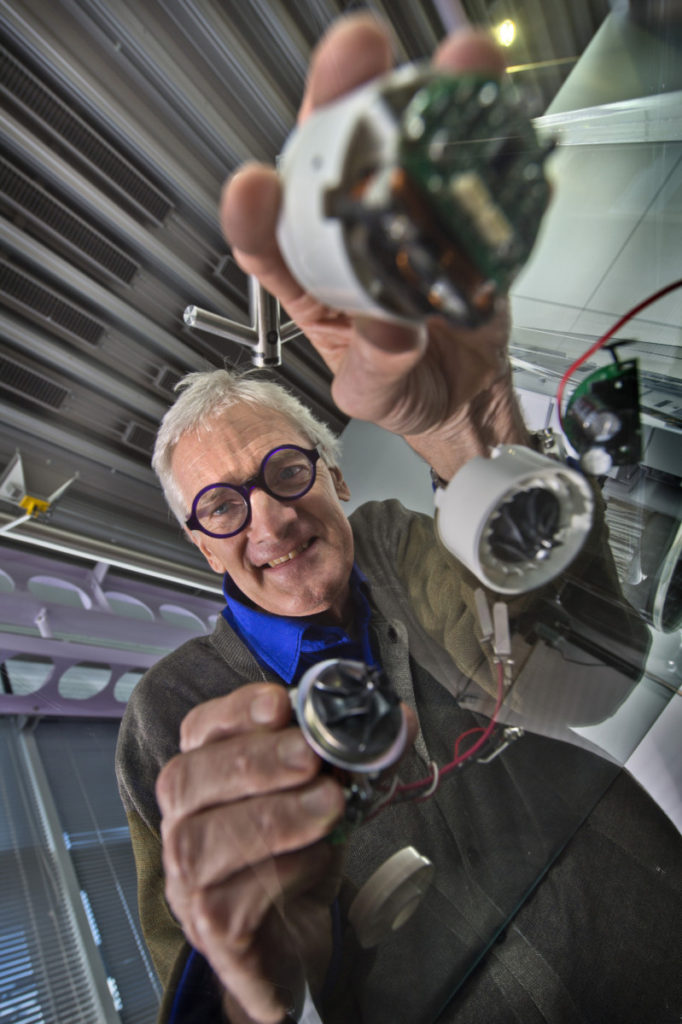
Sir James Dyson with examples of Digital Motors that go into a host of his products
Sir Dyson then added “ We’ve started building an exceptional team that combines top Dyson engineers with talented individuals from the automotive industry. The team is already over 400 strong, and we are recruiting aggressively. I’m committed to investing £2bn on this endeavour.” In current day figures, that’s about RM10,885,137,585 give or take some pocket change. Dyson has also invested in a huge proving ground at Wiltshire that consist of a 10-mile test track and more.
And with that, he bade goodbye to us before addressing another meeting even as we strode back to our waiting vehicles, diesel powered, alas, that would send us back to Kuala Lumpur. KT